Deep Injection of S-MicroZVI & 3DMe for Haley and Aldrich
- toddwhanna
- Aug 19, 2021
- 4 min read
Updated: Mar 8, 2023

The Legacy Remediation team recently wrapped up a 6-week ISCR-Enhanced Bioremediation Injection project in Northern Los Angeles County, California for Haley & Aldrich. The primary COC is trichloroethene (TCE) followed by some tetrachloroethene (PCE), but at much lower concentrations.
Haley & Aldrich designed three (3) strategically located permeable reactive barriers to treat the TCE and other VOCs in three vertical treatment zones, after using MiHPT Membrane Interface Probe and the Hydraulic Profiling Tool data to delineate impacts. Prior EISB efforts have greatly reduced the size and concentrations of TCE, and the potential environmental risks.
Haley & Aldrich obtained approval from the Regional Water Board Clean Up and Permitting Units. Facing complex injection requirements and challenges injecting at deep depths due to subsurface conditions, H&A chose to team with Legacy Remediation and Veteran Drilling, a firm with years of experience, expertise, and purpose-made equipment. This partnership increased the chances of successfully implementing the injection of Zero-Valent Iron S-MicroZVI, 3-D Microemulsion and BDI Microbial Consortium, all provided by Regenesis.

The Legacy team mobilized one of our standard dual-purpose Geoprobe Transport / Self-Contained Injection Trailers.

We also mobilized our support truck loaded with tools and equipment, along with our pneumatic tire field forklift.

Regenesis delivered the Sulfidated Zero-Valent Iron, S-MicroZVI in 2,000 lb IBC Totes. S-MicroZVI is a zero-valent iron (ZVI) product used to accomplish In Situ Chemical Reduction (ISCR) of contaminants. It is delivered as a colloidal suspension 40% ZVI by weight in glycerol with a particle size of less than 5 microns. It is manufactured with a sulfidation process resulting in a particle coating which increases activation toward specific contaminants and extends performance and longevity.

The 3-D Microemulsion was also delivered in 2,000 lb IBC Totes.
3DMe is a factory blended Electron Donor Emulsion used for Anaerobic Biodegradation of Chlorinated Compounds.
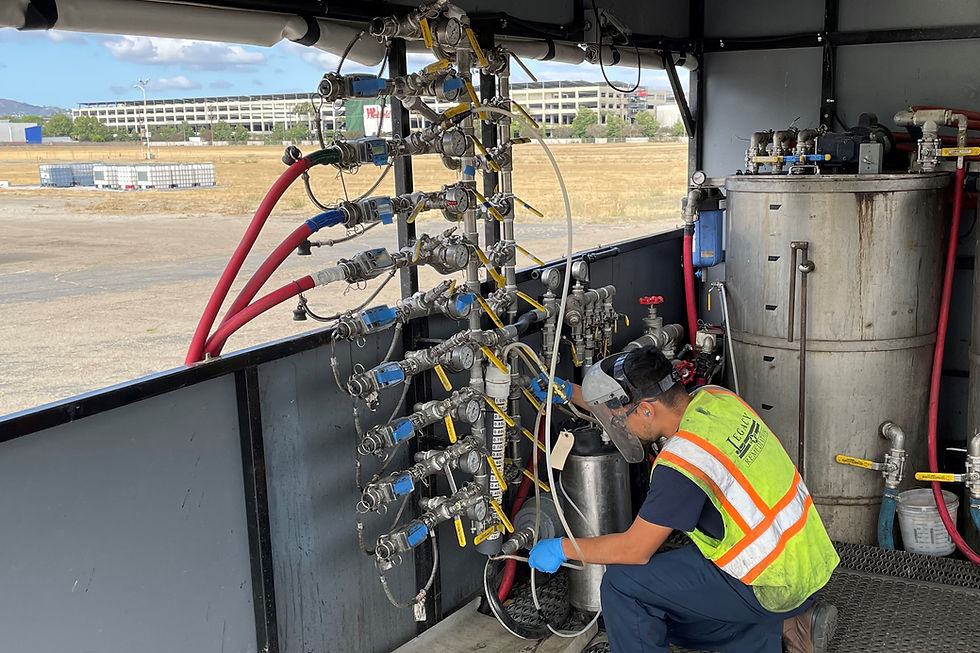
We bioaugmented with the BDI Microbial Consortium, it was injected directly into our 10-point injection manifold to eliminate oxygen exposure to the anaerobic microbes.

Our mix water came from two (2) nearby fire hydrants, depending on where we were located onsite.
Legacy coordinated with LADWP to get the meter and backflow device installed.
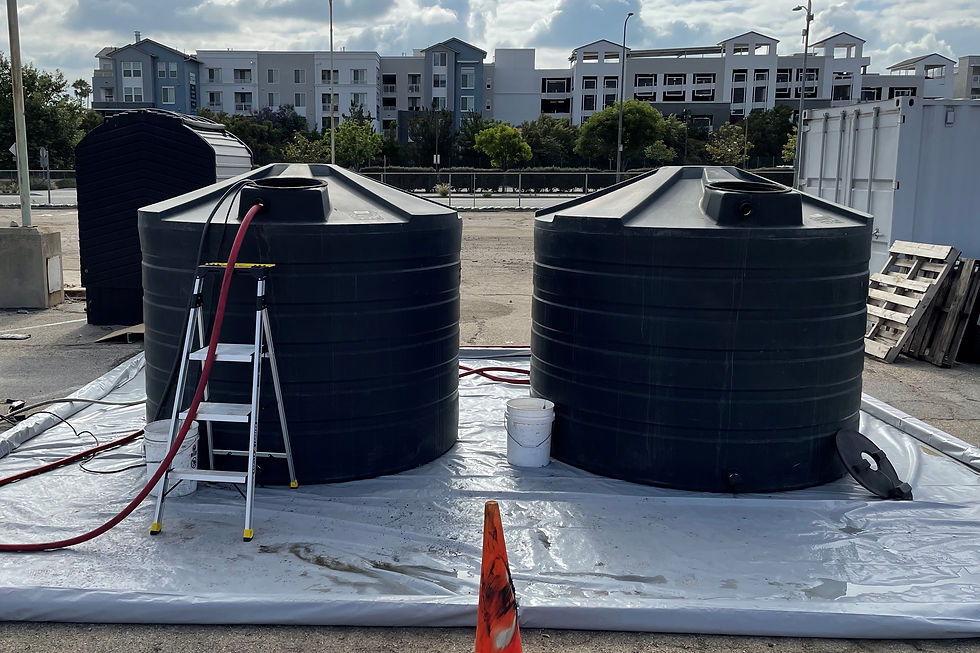
Anaerobic water was injected before and after each BDI dose.
To make up the necessary anaerobic water, we simply added S-MicroZVI to the hydrant water in poly tanks, and allowed time for the water to turn anaerobic.
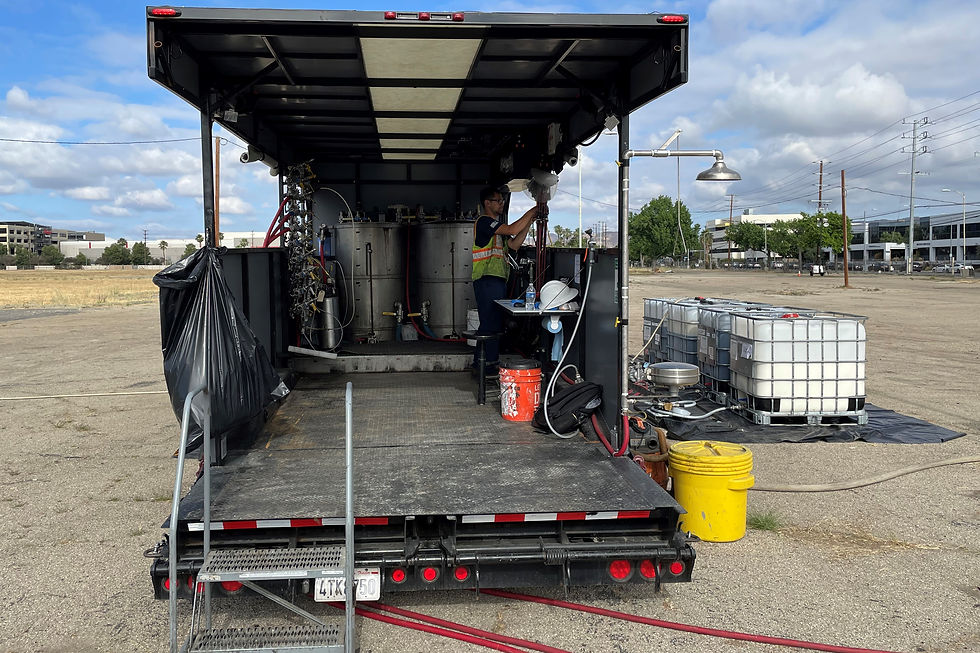
We mixed the S-MicroZVI and 3DMe in alternating batches in our 150 gallon Stainless Steel Mix Tanks.
The S-MicroZVI and 3DMe was mixed and injected at 10 different concentrations, depending on the area and treatment zone.
The project scope of work was made up of 82 Direct Push Injection Points and 19 Injection Wells. We injected into three target treatment zones (upper, intermediate and deep). Depending on the area, injections began as shallow as 20 feet bgs, and extended as deep as 104 feet.

From previous experience on this project, we know that it starts getting slow for Geoprobes around 60 feet, and they start having trouble below 85 feet. For this project we teamed with our friends at Veteran Drilling who brought out one of their CPT trucks to advance the Injection Tooling.

Between the static weight of the Veteran CPT Truck, and the optional Direct Push Hammer, we were able to quickly advance the Injection Tooling to the target treatment zone.

We also had one of our Geoprobe 7822DT’s onsite. The 7822DT was used primarily to remove the injection tooling, then advance grout rods to total depth, for bottom-up pressure grouting with Portland Cement/Bentonite Grout Slurry. The grout was mixed and pumped using our grout plant mounted to the 7822DT drop rack. The bottom-up pressure grouting was done to avoid the potential for creating conduits and cross-contamination.

We ran up to 5 points simultaneously through our 10-point dual injection manifold. With this manifold design, the injection points do not need to stay on the same schedule. Some points could be getting the ZVI/3DMe mixture, while others were getting BDI and Anaerobic Water.

We had ten (10) different S-MicroZVI and 3DMe mixture concentrations, and each point could get up to 3 different mixture concentrations, depending on the depth. We had to plan ahead to make sure we were optimizing our efforts at all times.

To help maximize our efforts, at any given time we would have 8 or so sets of injection tools in the ground ready, so we always had points available to inject on.

Clean injection tools are an important step in keeping them working well. Having our decon trailer onsite allowed us maintain a surplus of clean and ready tools, and it made for easy recovery the decon fluids.
This project had a lot of moving parts, it required a lot of communication between client and crew. Among our crew, we had to coordinate many onsite tasks and manage multiple pieces of equipment. Weather was one of the biggest challenges on this project, we routinely had 100 degree days, with some days nearing 110 degrees. Despite these challenging site conditions, high temperatures, and managing Covid-19 Pandemic, the Legacy and H&A team completed the job safely and without incident.

If you have any questions about this project, please feel free to contact the design consultant Thomas Tatnall at (714) 709- 3722 or via email at TTatnall@haleyaldrich.com, if we can help support any of your current or upcoming projects please contact us.
This post can also be viewed on our LinkedIn. Follow Legacy Remediation on LinkedIn to stay up to date on upcoming projects.